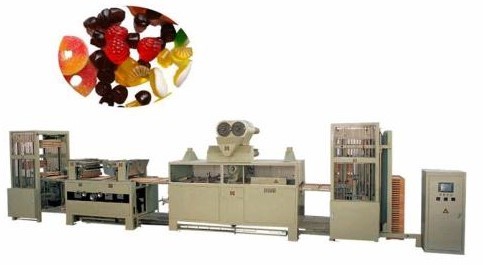
Types of the possible products:
Starch, gelatin or pectin jellies etc;
Deposited marshmallow ( additional devices needed);
one-color, two-color, two-layer or sandwich etc.
with or without fillings ( special filling pump needed);
GF STARCH MOULDING PLANT ( GF-MG-30/NM):
Tray size: 820×400×56mm
Pallet: Double Stacks, totally 80 trays.
Speed: One tray (720 pieces) deposited at one stroke; up to 30 trays per minute for standard products, depending on candy material, product shape and starch condition.
Capacity: 8000kg/shift (depends on candy sizes)
Power: 105Kw(depends on the final configuration of the plant)
Electrical equipment: to be confirmed by the customer.
Steam: 7~8bar; 850kg/hr
Compressed air:0.6Mpa, 300m3/hr
Water(<10℃):315kg/min
Workshop Area: Approx. 150 m2
STANDARD CONFIGURATION
Item 1: AUTOMATIC TRAY FEEDER
Straight end-entry pallet run-in rails accepting pallets delivered by forklift. The loaded pallets are automatically drawn into the Feeder Loading Platform by full-stack height selecting gates which straighten the stacks and provide support from the rear for safe and smooth transfer. Full-stack-height rollers guide the sides of each stack. Sub-stacks of five trays are lifted up by heavy duty clamps acting on each side of the trays, the clamps being carried by 1″pitch roller chain, and are presented to the feed position of the starch section. By lifting cam, the trays are taken one at a time by the feedbar system into the starch section. Separate motor drives are provided for pallet run-in and for the clamp-carrying chain. Clamping action is controlled by proximity switch and cam rollers, while intermittent motor stoppage by Warner/Electric Clutch Brakes. Motor drives are protected by torque limiter clutches.
Item 2: STARCH SECTION
Tray transport through starch section is by mechanical walking-beam with the alignment of feedbars maintained by free-running ball races and rollers combining flat-faced rolling surfaces with tapered aligning rollers. Tray emptying is by two pairs of arms each incorporating a self-centering pneumatic clamping system which rotates the tray through 180 degrees.
Starch and goods released from the inverted tray drop into a stainless steel chute, guiding them through a large diameter revolving drum screen combined with a rotary brush. The cleaned goods are discharged on to an output conveyor.
The moulding starch is collected from the base of the machine and transported by a motorized screw conveyor to a twin-barrel starch sifter mounted above the tray filling position. After passing through the sifter, the starch will be directed to the Starch Conditioning System and returned to the tray filling position after drying and cooling.
Tray filling is from a hopper beneath the sifter through an adjustable gate. A rotary feeding starch paddle, and a level control skimming spiral are combined to achieve a controlled starch level in the hopper, which results in trays filled with well aerated starch of even density. After filling the starch in the tray is leveled by a series of “V” shaped ploughs, gently displacing surplus starch towards the side of the tray and into the base of the machine for recirculation. Sides of tray are cleaned by brushes.
Tray printing is effected when the tray is stationary by a four-post printer table carrying the moldboard. A controllable pneumatic vibration mechanism is provided to free the moulds from the starch before the mould board is lifted. Moldboard is held by quick acting lever clamps and can be slid into place by one man from the side of the machine. Adjustments for printing depth and stroke are provided.
There’re two sets of mouldboards which are made of all-metal teflon coated aluminum. Moulds design can be made as per request of customer.
All mechanical motions in the starch section are synchronized and interconnected and are taken from the main Gearbox in the Depositor Section. Drives are protected by torque limiter clutches. Pneumatic Cylinder clamps in Tipper Arms are actuated by solenoid valves related to tray movement.
Item 3: DEPOSITING SECTION
This section is designed to accommodate two depositing pumps, with each pump operating at one stroke per tray. The depositing process is carried out when there’s no relative movement between the nozzles and the tray. The tray under the pump will be pushed up to accept depositing and will fall down after being deposited, which perfectly solves the possible problem of tail with the deposited candies. In this section, there’re two positions for the trays to be deposited:
No. 1 Depositing Position will be arranged for depositing single layer articles at 1 colour per tray. Exact pump configuration is subject to review of the desired candy articles, but for the purpose of this offer the pump is assumed to be 18 row x 40 pistons with 9 mm piston diameter, which can deposit 720 pieces of candies at one stroke. The pump will be equipped with two hoppers, both of which are equipped with water jacket for heating by steam. (Electric heating is possible). Each hopper is divided into three compartments and three different colors candies can be deposited at one time. A sensor ensures that if there’s no tray in due position, the pump shall not deposit. Moreover, the nozzles are able to suck back certain amount of candy mass after depositing and the mass amount is able to be pre-set.
No. 2 Depositing Position will be arranged for depositing single layer articles at 1 colour per tray. Exact pump configuration is subject to review of the desired candy articles, but for the purpose of this offer the pump is assumed to be 18 row x 40 pistons with 9 mm piston diameter, which can deposit 720 pieces of candies at one stroke (360 pieces if with center filling). The pump will be equipped with two hoppers, both of which are equipped with water jacket for heating by steam. (Electric heating is possible). Each hopper is divided into three compartments and three different colors candies can be deposited at one time. A sensor ensures that if there’s no tray in due position, the pump shall not deposit. The nozzles are able to suck back certain amount of candy mass after depositing and the mass amount is able to be pre-set. If the customer wants to produce two layer candies, this pump can be used to deposit second layer on top of the first layer deposited by the pump in No. 1 Depositing Position. The normal depositing pump, SERVO controlled center filling pump and marshmallow pump can be selected in this position. Main drive and tray conveyor drive are protected by torque limiter clutches.
Both pumps in above two positions are equipped with one Nozzle plate, one metal Piston Plate and 720 pieces Piston Bars. The Piston Bars do not need interchanging for different deposit patterns. The depositing amount at No.1 Depositing Position is adjusted mechanically while the depositing amount and timing at No. 2 Depositing Position are adjusted through independent geared SERVO motor. All pumps have hollow-body design, manufactured in stainless steel for superior resistance to chemical and mechanical wear. Internal pump heating is by circulation of hot water from the hopper water jacket.
One set of SEW motor and reducer from Germany has been installed in Depositing Section.
There is a starch sprinkler mounted on the rails between the Depositing section (Item 3) and Automatic Tray Stacker (Item 4 as below), with manual starch re-fill. The Sprinkler delivers a thin layer of starch on top of the deposited trays. This is useful for drying certain confectionery masses or for demoulding candy shapes with large flat surface area.
Item 4: AUTOMATIC TRAY STACKER
Linear run-out rails for twin-stack pallets. Construction similar to Feeder (Item 1), and ejection of the loaded pallet is made automatically when both stacks have been built to the required height.
Item 5: ONE SET OF BRUSHLESS CANDY CLEANER
A strong fabricated frame is mounted on adjustable height legs with castors. The frame carries a conveyor belt of balanced weave wire belting 400mm wide, passing around two open-cage pulleys. Two pairs of spinners are mounted, above and below the belt, air driven with air jets directed towards the belt, Each pair has a dust collection cone with external outlet for connection to the free-standing Dust Collector. Complete with motor drive, switchgear and wiring.
Item 6: ONE SET OF DUST COLLECTOR
To serve Brushless candy cleaner and Starch Section. A free-standing cabinet Dust Collector with 32 square meter Filter area. Complete with motor and fan (with silencer) of 3000 CFM capacity. Reverse air jet sequential control for cleaning of filter bags.
Item 7: ONE SET OF OILING MACHINE
For oil polishing of jelly Candy. Stainless Steel revolving drum mounted on substantial fabricated steel frame and supported by large diameter plastic tyred rollers. Drum interior is designed with a series of welded flights to ensure random rolling of sweets as they progress from entry to exit, in continuous motion. Oil is dispensed by metering pump from a heated reservoir at an adjustable rate. Fitted with motor drive, switchgear and wired.
Item 8: ONE SET OF STARCH CONDITIONING SYSTEM
This system consists of one Drying cabinet and one Cooling cabinet, connected by motorized screw conveyor. Drying cabinet has two air intakes on each side of the machine, and each is fitted with two sets of 2-row Steam Coils. Steam valves, regulators and sensors are included. Integral top-mounted Dust Collector creates airflow of 8,000 CFM by 30KW motor, through the 60 sq. meter filter area. Filters are cleaned by sequential air pulse jets, returning starch to the system.
The cooling cabinet uses German WSD starch cooling system for reference and is completely redesigned according to original-used interfaces. The conditioning system consists of many stainless steel pipes. Each pipe is composed of spiral propeller which connects with cooling liquid. By means of cooling liquid into pipe jacket and spiral propeller, hot starch is cooled enough when going through this system. It can cool starch from 80℃ to 25℃.
Since the cooling system is fully isolated from outside air, it avoids that the starch humidity comes rising again and improves product quality quite a lot. It also settles the existing problems in NID’s starch cooling system which is easy to cause starch humidity rising again when cool air goes into cabinet from outside.
Item 9: PALLET UNDERFEED SYSTEM
Carries the empty pallets from the Feeder to the Stacker where they wait until stacked with trays. This system is fully synchronized and automatic. Once fully stacked, the pallet is ejected from the Stacker onto the rails of the Run-out, where it is picked up by the operator with a lift truck.
Item 10: ELECTRICAL EQUIPMENT
It is fully wired and integrated before dispatch with locking plug-in wiring sockets at each section. PLC Control Cabinet with “Siemens” PLC(S7) will control the complete line, and will include a mimic display board to highlight location of any stoppage. One digital panel can display line speed, deposit volume and suckback volume.
OPTIONS:
1. ONE SET OF CENTER FILLING PUMP CONTROLLED BY SERVO MOTOR WITH ALL THE NECESSARY MODIFICATION ON THE DEPOSITOR
--The center filling pump is controlled by two sets of YASKAWA SERVO motors from Japan. Through PLC, the SERVO motors are able to adjust the depositing amount of both center mass and outer mass to ensure precise and stable depositing with fillings. The positions of center fillings inside the candies can be accurately adjusted too according to customers’ requirements. The Piston Plate adopts compound design featured as compact structure, stable movement and easy disassembling. When depositing, the timing and suckback volume can be controlled through PLC, which ensures accurate depositing and less tail. Upon this pump, both candies with or without center fillings can be deposited.
The depositing pump for marshmallow is the same as for center filled candy but the whole system is with complete airproof design including the Airproof Hopper and the Airproof Pipes. The candy mass will flow in complete airproof pipes and hopper, which can ensure the smooth flow of candy mass with poor fluidity for the purpose of smooth depositing. Upon this pump, both candies with or without center fillings can be deposited.
2. ADDITIONAL ONE SET OF METAL MOULDBOARD
3. ADDITIONAL ONE SET OF STANDARD NOZZLE PLATE:
PART TWO: GF COOKING SYSTEM FOR JELLY
It is suitable for the continuous cooking of jelly. It includes following equipments:
a. Two sets of jacketed stainless steel vessels of 100 litres each: to dissolve gelatins into liquid state by high speed stirring;
b. One set of jacketed stainless steel vessel of 20 litres: to dissolve pectin into liquid state by high speed stirring.
c. Two sets of jacketed stainless steel vessel of 250 litres each with low speed of stirring: to dissolve sugar, glucose syrup and water into the form of sugar syrup. It is connected with a discharging pump with screws.
d. Two sets of mixing stainless steel vessels of 250 litres each with high speed stirring: to mix the sugar syrups with gelatin/pectin syrups.
e. Continuous vacuum cooking system with capacity of up to 1000kg/h: the syrups inside the cooker shall be cooked fast and continuously to required consistency, which can ensure the colloid to be fully protected during the cooking process. The system consists of following equipments each one set:
1) Stainless steel Infeed pump with mechanical speed-adjustment;
2) Stainless steel high speed vacuum cooking device;
3) stainless steel vacuum vessel ;
4) stainless steel pump which can discharge syrups under conditions with 60~70% vacuum; with variable speed adjustment
f. Fragrance adjusting system which can adjust fragrance and color in the pipes continuously and automatically according to the proportion to ensure superior quality of the final products. The system includes:
1) Four sets of stainless steel buffering vessels of 200 litres with liquid level sensor;
2) Two sets of stainless steel vessels for flavors;
3) Two sets of stainless steel vessels for colors and acids;
4) Two sets of stainless steel triple-expansion pumps;
5) One set of stainless steel pipe-shaped blender for blending of all above materials.
SPECIFICATION:
Capacity: 8000kg/shift
Power: 105kw
Steam: 8~10bar: 850kg/hr